APQP เป็นกระบวนการที่กำหนดไว้สำหรับการพัฒนาผลิตภัณฑ์ในอุตสาหกรรมต่างๆ โดยเฉพาะยานยนต์ ประกอบด้วยขั้นตอนและเทคนิคต่างๆ โดยมีวัตถุประสงค์เพื่อพัฒนาแผนคุณภาพที่เป็นประโยชน์ต่อการพัฒนาผลิตภัณฑ์และตอบสนองความต้องการของลูกค้า เช่นเดียวกับ PPAP, SPC, MSA และ FMEA APQP ถือเป็นเครื่องมือหลักของภาคยานยนต์
ในบทความนี้คุณจะพบ:
APQP คืออะไร?
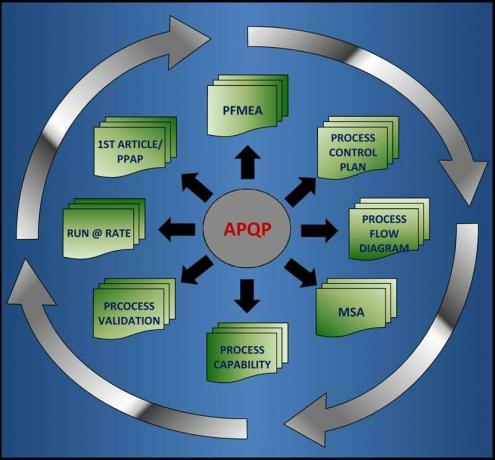
โฆษณา
APQP (การวางแผนคุณภาพผลิตภัณฑ์ขั้นสูง) เกิดในปี 1980 โดยได้รับมอบหมายจากบริษัท Ford, Chrysler และ GM ตั้งแต่นั้นมาพวกเขาได้ใช้เครื่องมือนี้ รวมถึงซัพพลายเออร์และบริษัทในเครือบางแห่ง
ใช้เป็นแนวทางในการพัฒนาและเชื่อมโยงระหว่างบริษัทยานยนต์และซัพพลายเออร์ เป็นวิธีที่มีประสิทธิภาพในการแบ่งปันผลลัพธ์
โฆษณา
ขั้นตอนของ APQP
APQP มุ่งเน้นที่ การพัฒนาผลิตภัณฑ์ใหม่สำหรับการพัฒนาอุตสาหกรรมและการเปิดตัวตลาดในภายหลัง ประกอบด้วยชุดของขั้นตอนต่างๆ ที่มีการวิเคราะห์รายละเอียดทั้งหมด เช่น การออกแบบ ความทนทาน การปฏิบัติตามฟังก์ชัน การตรวจสอบคุณภาพ ฯลฯ
จำเป็นต้องวิเคราะห์กระบวนการเหล่านี้อย่างละเอียดเพื่อให้ผลลัพธ์เป็นบวก
โฆษณา
1. กำหนดโปรแกรม
ผู้มีโอกาสเป็นลูกค้าจะได้รับการศึกษาเพื่อกำหนดความคาดหวังของพวกเขา เพื่อดำเนินการออกแบบและการทำงานของผลิตภัณฑ์ขั้นสุดท้าย มีการใช้เครื่องมือต่างๆ เช่น รายการ การระบุแง่มุมในอุดมคติที่ผลิตภัณฑ์ควรมี ตลอดจนไดอะแกรมที่แสดงกราฟการไหลของกระบวนการผลิต
ด้วยเหตุนี้ ผลิตภัณฑ์จึงสามารถทำอย่างละเอียดได้ โดยมีลักษณะเฉพาะที่จำเป็นสำหรับการผลิต ซึ่งรับประกันคุณภาพขั้นสุดท้าย แต่ละแผนกมีบทบาทสำคัญ แม้จะมีลักษณะและความรับผิดชอบต่างกัน
โฆษณา
2. ออกแบบและสร้างผลิตภัณฑ์
ทีมงานที่รับผิดชอบในการเฝ้าติดตามและตอบสนองต่อปัญหาต่างๆ ธุรกิจมักเรียกมันว่า "โหมดความล้มเหลวในการออกแบบและวิเคราะห์" และประกอบด้วยการระบุแนวทางและวิศวกรรมที่แตกต่างกัน สิ่งสำคัญคือต้องตรวจสอบทุกรายละเอียดในการพัฒนาต้นแบบแรก เพื่อให้สามารถปรับข้อบกพร่องได้ทันเวลา ก่อนเริ่มการผลิตจำนวนมาก
ทีมวางแผนมีหน้าที่ตรวจสอบคุณภาพของทีม ต้องมีการกำหนดข้อกำหนดพื้นฐาน กำหนดจุดสำคัญของผลิตภัณฑ์และการผลิต โดยได้รับการสนับสนุนจากภาคการบริหาร
โฆษณา
3. ปรับกระบวนการผลิต
ทีมงานให้ความสำคัญกับองค์ประกอบที่เป็นส่วนหนึ่งของกระบวนการผลิต เนื่องจากมีวัตถุประสงค์เพื่อรับประกันผลลัพธ์ที่ดี ในขณะที่ยังคงประสิทธิภาพและประสิทธิผลไว้ ต้องหลีกเลี่ยงความล้มเหลวในการออกแบบและวิธีการ หลายบริษัทเรียกกระบวนการนี้ว่า "เอฟเฟกต์โหมดความล้มเหลว"
จากการวิเคราะห์ระบบ ทีมงานจะปรับแผนหากจำเป็น ในทางกลับกันพวกเขาจะรับผิดชอบในการพัฒนาแผนที่จะรับผิดชอบข้อกำหนดและรายละเอียดของบรรจุภัณฑ์
4. การตรวจสอบผลิตภัณฑ์
ขั้นตอนที่สี่ประกอบด้วยการทดสอบการผลิต จุดประสงค์คือเพื่อดูว่ากระบวนการได้ดำเนินการอย่างถูกต้องหรือไม่ ผลลัพธ์เป็นไปในเชิงบวกหรือหากมีความล้มเหลวในขั้นตอนใดขั้นตอนหนึ่ง การทดสอบนี้มีความสำคัญอย่างยิ่ง โดยใช้เครื่องมือวัดเพื่อศึกษาส่วนประกอบและผลิตภัณฑ์อย่างแม่นยำ
5. การประเมินและการแก้ไข
แน่นอนว่าแผนอาจแตกต่างกันไปและไม่มีใครถือว่าสมบูรณ์แบบ ด้วยเหตุนี้ ระยะสุดท้ายจึงประกอบด้วยการปรับเปลี่ยนที่ต้องทำเพื่อปรับปรุงผลิตภัณฑ์ การศึกษาที่ดำเนินการจะช่วยในการตัดสินใจที่ถูกต้อง ไม่ว่าจะแก้ไขหรือปรับปรุงผลลัพธ์
คุณภาพจะขึ้นอยู่กับความจุและวัตถุประสงค์ที่ตั้งไว้ก่อนหน้านี้ การดำเนินการแก้ไขอาจเป็นกระบวนการส่วนกลางทั้งหมด หรือบางขั้นตอนเท่านั้น ไม่ว่าการเปลี่ยนแปลงผลิตภัณฑ์จะเป็นอย่างไรเพื่อตอบสนองความต้องการของลูกค้า
ตัวอย่าง APQP
บริษัทขนาดใหญ่ทั่วโลกใช้แผนประเภทนี้ ทุกวันนี้บริษัทแรกๆ ที่ใช้บริการยังคงรักษาคุณภาพการบริการ และทำให้ลูกค้าไว้วางใจและยอมรับ ได้แก่ Ford, General Motors และ Chrysler
หลายบริษัทใช้แผนประเภทนี้เพราะช่วยให้สามารถพัฒนาผลิตภัณฑ์ตามแนวโน้มของตลาดได้ แม้ว่าจะมีการเปลี่ยนแปลงครั้งใหญ่ในต่างประเทศก็ตาม
ตัวอย่างที่สำคัญที่สุดบางส่วน ได้แก่ บริษัทที่อยู่ในสายเทคโนโลยี เช่น Apple เพราะพวกเขาต้องการกลยุทธ์ที่ช่วยให้พวกเขาปรับให้เข้ากับข้อกำหนดของพวกเขา ลูกค้า. ด้วยเหตุนี้จึงเป็นเรื่องปกติที่บริษัทต่างๆ จะออกแบบและเปิดตัวผลิตภัณฑ์ในช่วงเวลาสั้นๆ